QR Code
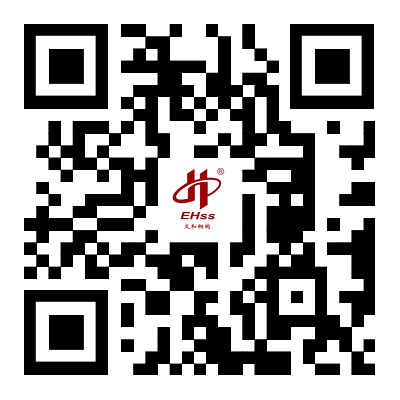
Products
Contact Us
Phone
E-mail
Address
No. 568, Yanqing First Class Road, Jimo High-tech Zone, Qingdao City, Shandong Province, China
A large amount of steel is needed in the design of steel structure project, but if the steel used in construction rusts a lot, it will greatly shorten the service life. For personal safety is also a challenge, the collapse of the house is common, in recent years more and more attention, today Fangtong steel structure will teach you some rust removal methods!
1、Descaling by pickling
It is to put the steel member to be painted in the acid pool, and remove the oil and rust on the surface of the member with acid. The efficiency of the pickling process is also high, and the rust removal is more thorough, but after pickling, the components must be rinsed with hot water or water, and if there is residual acid, the corrosion of the components will be more powerful.
2、Descale manually
It is to remove the rust on the steel components by manual labor with some relatively simple tools, such as scraper, grinding wheel, emery cloth, wire brush and other tools. This method has low working efficiency, poor labor conditions and incomplete rust removal.
3、Sandblast and descale
It is the use of compressed air pressure, continuous quartz sand or iron sand impact on the surface of steel components, the surface of the steel rust, oil and other debris clean up, revealing the metal steel color of a rust removal method. This method has high efficiency, removes rust thoroughly, and is a more advanced rust removal process.
How to classify the steel structure rust grade?
Construction method |
Characteristics of Applicable Coatings |
coatings |
Use of tools or equipment |
Main advantages and disadvantages |
||
Drying speed |
Viscosity |
Variety |
||||
brushing |
Dry and slower |
low plasticity |
Oil-based paints Phenolic paint Alkyd paint, etc. |
General components and buildings, various equipment piping, etc. |
Various brushes |
Low investment, simple construction method, suitable for all kinds of shapes and sizes of the area of the coating; drawbacks are less decorative, low construction efficiency |
Hand rolling method |
Dry and slower |
low plasticity |
Oil-based paints Phenolic paint Alkyd paint, etc. |
Components and management of large planes in general, etc. |
rollers |
Less investment, simple construction method, suitable for large area coating; drawbacks with the brush coating method |
dip coating |
Appropriate dryness, good leveling, moderate drying speed |
Good thixotropy |
Various synthetic resin coatings |
Small parts, equipment and machine components |
Paint dipping tanks, centrifugal and vacuum equipment |
Less investment in equipment, simple construction methods, less loss of paint, suitable for the construction of complex components; the disadvantage is that the leveling is not very good, there is a phenomenon of hanging phenomenon, pollution phenomenon, the solvent is easy to volatile |
air spraying method |
Fast evaporation and moderate drying |
low viscosity |
Various nitro lacquers, rubber lacquers, construction vinyl lacquers, polyurethane lacquers, etc. |
Various large components and equipment and piping |
Spray guns, air compressors, oil/water separators, etc. |
Smaller investment in equipment, more complex construction methods, construction efficiency is higher than the painting method; the disadvantage is that the consumption of large doses, pollution phenomenon, easy to cause a fire |
mist spraying |
Coatings with only high boiling solvents |
Highly nonvolatile, thixotropic |
Paste-based coatings and high nonvolatile coatings |
Various large steel structures, bridges, pipelines, vehicles, ships, etc. |
High-pressure airless spray guns, air compressors, etc. |
Larger investment in equipment, more complex construction methods, higher efficiency than the air spraying method, can obtain a thick coating; the disadvantage is that it also needs to lose part of the paint, less decorative |
No. 568, Yanqing First Class Road, Jimo High-tech Zone, Qingdao City, Shandong Province, China
Copyright © 2024 Qingdao Eihe Steel Structure Group Co., Ltd. All Rights Reserved.
Links | Sitemap | RSS | XML | Privacy Policy |
Teams